How to Choose an Infrared Imaging Camera?
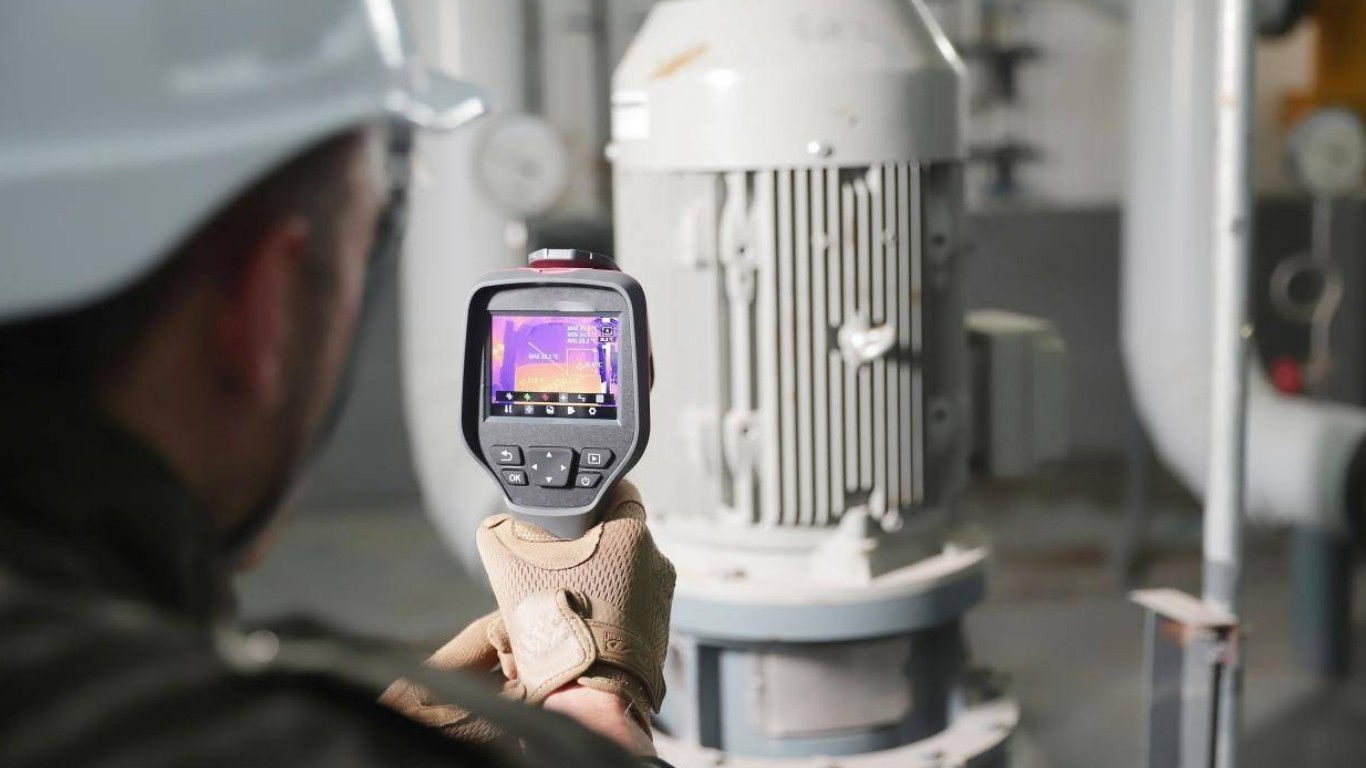
Before choosing an infrared camera, users must understand several factors, especially the different types of infrared detectors, cameras, and specifications, and how they affect system performance. There are many factors to consider in terms of temperature changes, shutter speed, and the ultimate cost and value of a thermal camera.
Precise measurement
It is relatively easy to understand relative temperature changes in a color-mapping camera because warmer colors tend to be warmer temperatures (red, orange, yellow) and cooler colors tend to be cooler temperatures depending on the palette settings (green, blue, purple).
The system provides a comprehensive view from cold to hot in an easy-to-read visual interface. However, if accurate temperature measurements are required, several potential sources of error must be considered: the emissivity of the surface, the viewing angle of the camera, the surface reflections and transmission characteristics of the target, atmospheric conditions, spatial resolution limitations, and motion blur. If one or more of these considerations are ignored, temperature accuracy will be severely compromised.
Reflection is another source of error. Hot objects near the target being measured may reflect off the target. Since the total temperature includes reflected energy, any reflections will mask the emitted energy and reduce measurement accuracy.
Depending on their physical properties, some targets may have transmission problems. Thermal cameras can see through certain types of materials, especially certain plastics. Therefore, it is important to ensure that large amounts of energy are not transmitted through the object being observed, otherwise, the temperature behind the target rather than the surface temperature may be detected.
Camera notes
A good thermal imaging camera has a temperature accuracy of about +/-20 degrees Celsius, or 2% of full scale, whichever is greater. Unfortunately, it doesn't matter if the camera costs $5,000 or $100,000, the accuracy isn't much better than +/-2℃. If more precise measurements are required, using a thermocouple may be a better option.
There is a reason for the huge price difference between calibrated and uncalibrated cameras. High-end thermal imaging cameras that are factory calibrated require precise temperature calibration in the laboratory. Such cameras also need to compensate for detector temperature drift, which requires temperature sensors and compensation electronics inside the camera. These features are usually not included in low-cost, uncalibrated cameras.
On most thermal imaging cameras, there is an aperture-type shutter to compensate for temperature drift. Periodically, a click may be heard from the camera, indicating that the shutter in front of the detector has closed and the camera is being recalibrated to compensate for thermal drift. This automatic calibration usually takes a few seconds and is performed during startup or when the camera detects an internal temperature drift. For automated imaging applications, this temperature recalibration needs to be considered because the camera is "blind" during recalibration and the continuous stream of image data will be interrupted. This is commonly referred to as NUC and can be done manually on multiple devices to ensure proper calibration of the devices.
NETD values
Noise Equivalent Temperature Difference (NETD) defines the detector's ability to distinguish small differences in thermal radiation in an image. Typical NETDs for uncooled microbolometers are less than 50 millikelvins (mK). Photon-based or cooled cameras with photon-based detectors provide temperatures better than 20mK. Therefore, if a high degree of measurement sensitivity is required, the camera may need to be cooled.
In cameras with multiple measurement ranges, NETD depends on the selected measurement range. The smaller the temperature range, the better the NETD. It is important to match the camera's NETD to the application, especially if lower temperatures need to be measured or the application requires higher temperature accuracy.
Application notes
When choosing a camera, it's important to understand the field of view, consider moving objects, and see through obstacles.
If you need to image a moving target, it is important to know how fast the target is moving in the camera's field of view, or more specifically, how far (in pixels) the target has moved in the integration time. This can cause motion blur when tracking moving objects. A sensor and core with a higher pixel resolution are recommended to provide a sharper image to avoid thermal smear.
The camera's lens is made of exotic and expensive materials such as germanium, zinc selenide, or sapphire, which transmit specific infrared wavelengths and match the camera's detectors. IR lenses are also curved aperture lenses, adding to the cost of manufacturing these high-quality and high-end optics.
The protective housing is also required when installing the camera in harsh environments. Since infrared cameras cannot see through standard glass windows, exotic germanium, zinc selenide, or sapphire windows are required for the camera housing. The window material must be matched to the specific camera and environment to allow heat transfer through the shield.
The above describes in detail how to choose an infrared thermal imager. If you want to buy an infrared thermal imager, please contact us.
JAVOL is a professional custom thermal imaging camera manufacturer. Relying on the multi-spectral high-sensitivity photoelectric sensor chip of advanced compound semiconductor materials, with deep learning AI algorithm as the engine, integrating low-light night vision technology, infrared thermal imaging technology, short-wave infrared technology and multi-spectral fusion technology, our company designs, develops and manufactures Advanced imaging products and system solutions are widely used in machine vision, autonomous driving, drone payloads, high-end manufacturing, and medical diagnosis.