What Are the Applications of Short-wave Infrared Cameras in High-temperature Manufacturing?
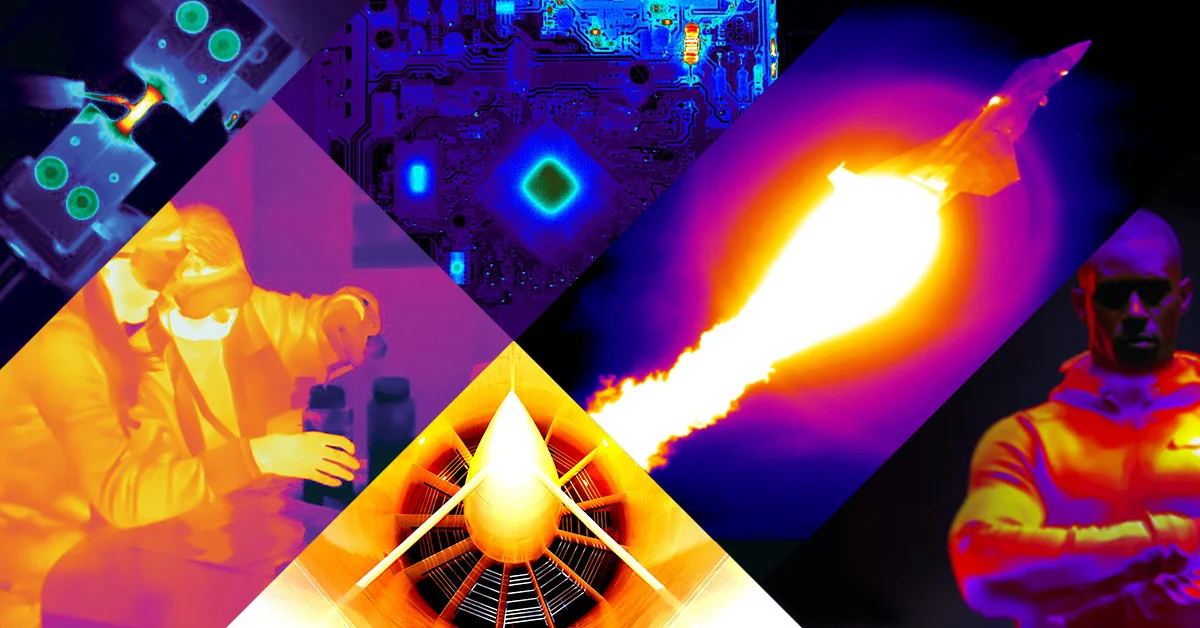
In recent years, short-wave infrared (SWIR) imaging technology has become more mature, and the response wavelength of short-wave infrared cameras is 0.9-1.7um. Prior to this, they were only used for qualitative imaging applications, such as laser beam profile, silicon wafer inspection, and imaging through paint/ink layers, not for actual quantitative temperature measurement applications.
Now, with the increase of the temperature measurement function, coupled with the shortwave infrared camera can easily penetrate the glass for observation, and in the case of emissivity changes, it can also accurately measure the temperature. The followings are the specific applications of short-wave infrared cameras in high-temperature manufacturing.
In high-temperature manufacturing, some special processes, such as metal processing and welding, occur in furnaces or environmental chambers designed to maintain specific atmospheric conditions. These chambers generally have windows made of ordinary silicon-based glass, which are opaque at longer wavelengths.
The current solution is to install windows made of materials such as zinc selenide or calcium fluoride in these chambers so as to be transparent to long-wave infrared or millimeter-wave infrared. But these materials are not only more expensive than silicon-based glass, but they may not be able to handle the environmental conditions of the chamber (such as heat, humidity, or vacuum) exactly like glass.
Another issue to consider is that the heat energy released by the material may vary. This change not only occurs between different materials but also occurs between the same material at different temperatures or different processing stages. These changes in emissivity will affect the accuracy of temperature measurement, and this effect is more pronounced at longer wavelengths than at shorter wavelengths.
The extension of the shortwave infrared camera temperature measurement function can provide solutions for customers who are concerned about the thermal analysis of high-temperature materials or processes.
In metal processing operations, the temperature during material processing is very important. For example, to manufacture steel plates, manufacturers start with a piece of molten metal and roll it back and forth on a rolling mill to achieve the required thickness. Throughout the process, steel needs to maintain a certain temperature, because compression at too low a temperature will change its material properties, resulting in the production of substandard steel.
3D printing technology is another process that requires high-temperature consistency. One way of working in 3D printing is to deposit a metal powder, then use a laser to quickly heat the powder, melt and fuse it into a solid. As with traditional steel manufacturing, the temperature at which the material is processed will affect its final performance.
In these applications, accurate temperature measurement of each process is very important for processes that require very high consistency. Using a short-wave infrared camera after temperature calibration, the user can obtain the complete thermal profile of the product. Because it can accurately measure temperatures up to 3000°C, there is no need to worry about missing the critical temperature threshold.
If you want to know more about short-wave infrared thermal imaging cameras after reading the above, welcome to contact JAVOL for a comprehensive solution.
JAVOL is an experienced manufacturer of infrared thermal imaging systems. We are equipped with a professional production team and quality inspection system to control the quality of the products in all directions. Our products are sold all over the world and used in all walks of life. We can also provide comprehensive customized services according to the needs of users. If you are interested in our shortwave infrared cameras, please contact us immediately!