Why Thermal Imaging Is Crucial for Detecting Moisture Damage
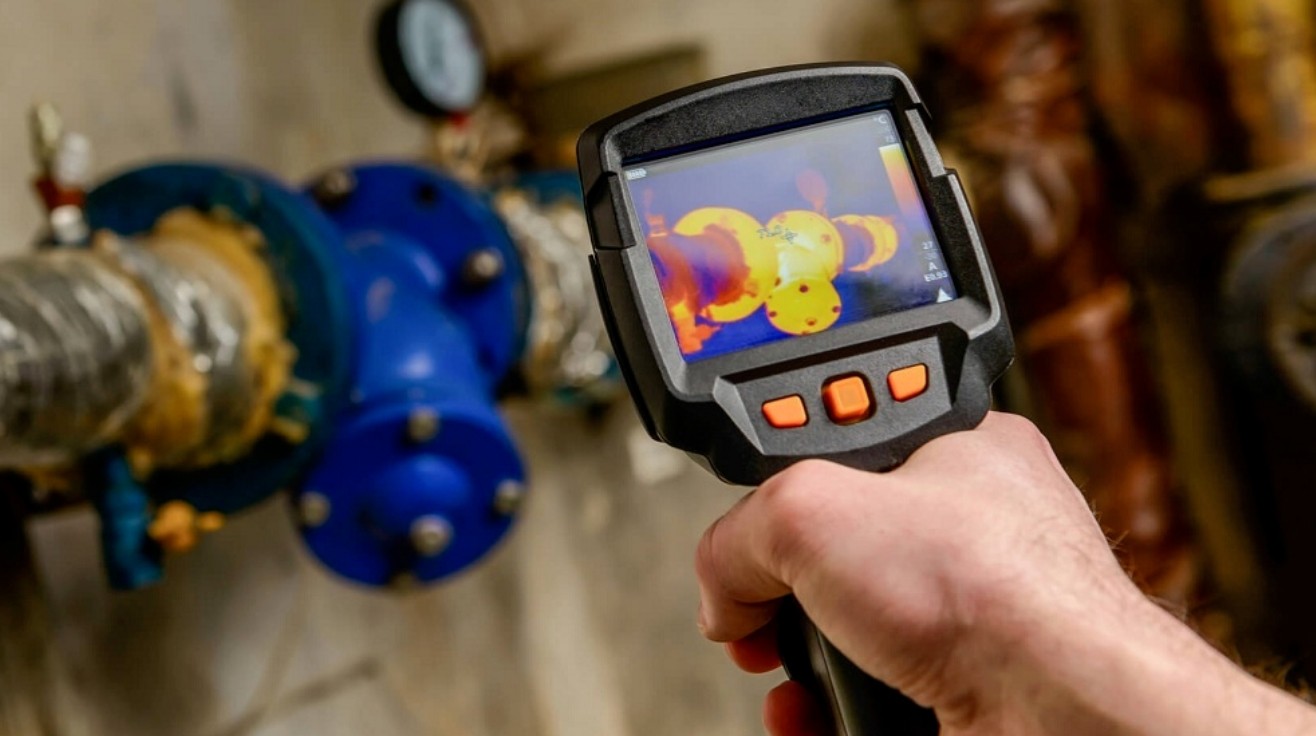
There are many areas where moisture can accumulate that are often overlooked during a typical inspection, or require extensive damage to the property to find them. That's why many people turn to thermal imaging as part of their building inspection regimen.
According to the U.S. Environmental Protection Agency, there is no practical way to eliminate mold spores from indoor environments. The best way to control mold growth is to control humidity, which you can use a thermal imager to detect. Finding leaks or water damage before mold has a chance to grow and spread can save time and money.
With the help of thermal imagery, insurance companies can better detect flood damage, reducing unforeseen conditions and subsequent requests for more mitigation. Due to properties such as heat capacity, thermal imaging cameras can show the presence of water beneath the surface, which is often the method of choice when finding faults on flat or low-slope roofs. The evaporative cooling effect is often the strongest indicator of moisture entering studs, insulation, and other interior wall components.
In the past, infrared technology has been successfully used to detect roof faults and in the fire protection and water restoration industries. With the technology available today, construction industry contractors can combine thermal imaging with their building inspection skills to make more meaningful and accurate assessments, with the added benefit of expanding their business.
Application of Thermal Imaging in Building Inspection
A forensic investigation is the process of uncovering building faults - whether it’s a homeowner complaining about a leaky roof, a business that just suffered a flood, or gathering data for a lawsuit. Typical areas where defects can be found include:
- Low, pitched roofs
- Electrical problems
- Plumbing or HVAC failure
- Insulation failure
- Any number of failed external components can result in water intrusion
Many components of building inspections and forensic investigations related to building failures or moisture issues can use a combination of traditional inspection techniques and infrared cameras. While an infrared camera may not be able to answer all of your questions, it can save homeowners a lot of time and money and help pinpoint problems faster and more accurately.
Traditional Water and Mold Tracking Methods
If a homeowner notices water on the carpet near a window, traditional methods of investigation may include "tracking" with an invasive or non-invasive moisture meter. This method will attempt to determine whether the water is passing through the wall, entering from a window, or flowing down the wall cavity from some other entry point. Ultimately, this will require some invasive means of investigation, such as cutting through the drywall to try and find the leak, opening the outer envelope to see the shimmering details, and adding water to replicate the behavior.
Using a thermal imaging camera, you can quickly and non-intrusively zero in on areas of possibility, making it easy to identify anomalies caused by evaporative moisture cooling. In the carpet example above, if the water came from the roofline or some other ceiling transition area, you would see the anomaly in multiple places or a continuous anomaly from the ceiling to the floor. Ultimately, the investigation may still require invasive action, but thermal imaging cameras can get to the leak or mold location more quickly and with less intrusion into the building envelope.
How to Conduct a Moisture Testing Survey
Before Starting the Investigation
Often, infrared inspection requests are made after the fact, so you don't see the problem at your best. When this occurs, water may need to be reintroduced to the potentially affected area. Before you start, be prepared to ask and answer some questions your client may have. What you learn about the history of the building will lead you to the area where water testing began.
You should ask the following questions about the building:
- How old is the building? (This gives an idea of the type of failure.)
- When did you first notice the problem? Is it during a rainstorm?
o Is it a heavy rain?
o Did you notice the problem after it rained for several days?
- If it is an exterior wall, that does not involve rain, is the landscape running against the same wall? Is there dirt on the outside of the printhead?
- Is this a multi-story unit? Is it directly under the bathroom or kitchen?
- What channels are there around the affected area? (i.e., is this a 3-4 story building?)
- Does it have extensive landscaping?
- Have you had any repairs recently? (e.g., roofing, painting, HVAC).
Some of the most frequently asked questions by investigators include:
- What if the spill dries before you can arrange it?
- IR camera survey only after rain?
- Can it see through anything (e.g. concrete, stucco, siding)?
- How long does it take?
- How much does it cost?
Start Survey and Water Testing
The next step was to prepare the interior to minimize any further damage and document the existing 'pre-test' condition of the affected areas using digital and thermal photographs with short descriptions. The process of setting up a pre-test scan with a thermal imaging camera is very simple. Since the camera can take not only thermal images but also photos and voice annotations, all the information you need before, during, and after your test can be organized and stored together.
To reintroduce water to an affected area, always start at the bottom and work your way up, unless evidence from an initial survey indicates moisture is coming from above (for example, roofs and ceilings are affected areas).
Always record start and stop times and move the water to each new location in eight to ten-minute increments. Water testing for a given area should not take longer than 30 to 45 minutes.
Once the leak is repeated, stop testing at that location. However, continue up the exterior wall to make sure there are no multiple locations. Take notes or voice records of the steps you are taking along with a short description of each hot photo. This is important because digital photos may be easily identifiable, and without annotations, thermal photos may not be meaningful later.
Watch the Weather for Success
It is also important to choose the optimal test time and maintain proper temperature control. Remember, the greater the temperature span from the outside to the inside of the building envelope, the better the thermal effect. To ensure a successful heat test, adjust your survey to weather conditions. For example, if it's very cold outside, you can control the temperature inside the building and turn up the heat.
Warm/hot climates are great for thermal studies because the air conditioning is cooling the inside of the building. The water used in the tests also tends to be cooler, which creates a greater temperature change, resulting in a better thermal image.
Also, pay attention to the type of material. Exterior materials such as stucco are more porous to absorb and retain moisture, providing a better exterior lens than siding that hides water behind planks of wood. You can also use hot water on the cold outside, but it won't be hot enough to find the problem.
Rely on Construction Industry Experience
Even if you've identified an area of concern, there's no harm in talking to an expert. Anomalies in the building envelope can easily arise, but if you do not have construction experience, consider working with a construction professional to help interpret the results. Save your comments in the report, as any verbal comments can easily be misinterpreted by laymen or homeowners, causing problems later.
The above content briefly introduces why thermal imaging is crucial to detecting moisture damage. If you want to buy a thermal imaging camera, please contact us.
With excellent production technology and considerate service, JAVOL has become one of the leading infrared thermal imaging systems manufacturer. Our professional production team and complete management system can meet the diverse needs of customers. We will continue to adjust and optimize new solutions according to customer needs, and provide customers with thoughtful one-stop service.