How Thermal Cameras Are Changing Welding and Metal Additive Manufacturing Processes
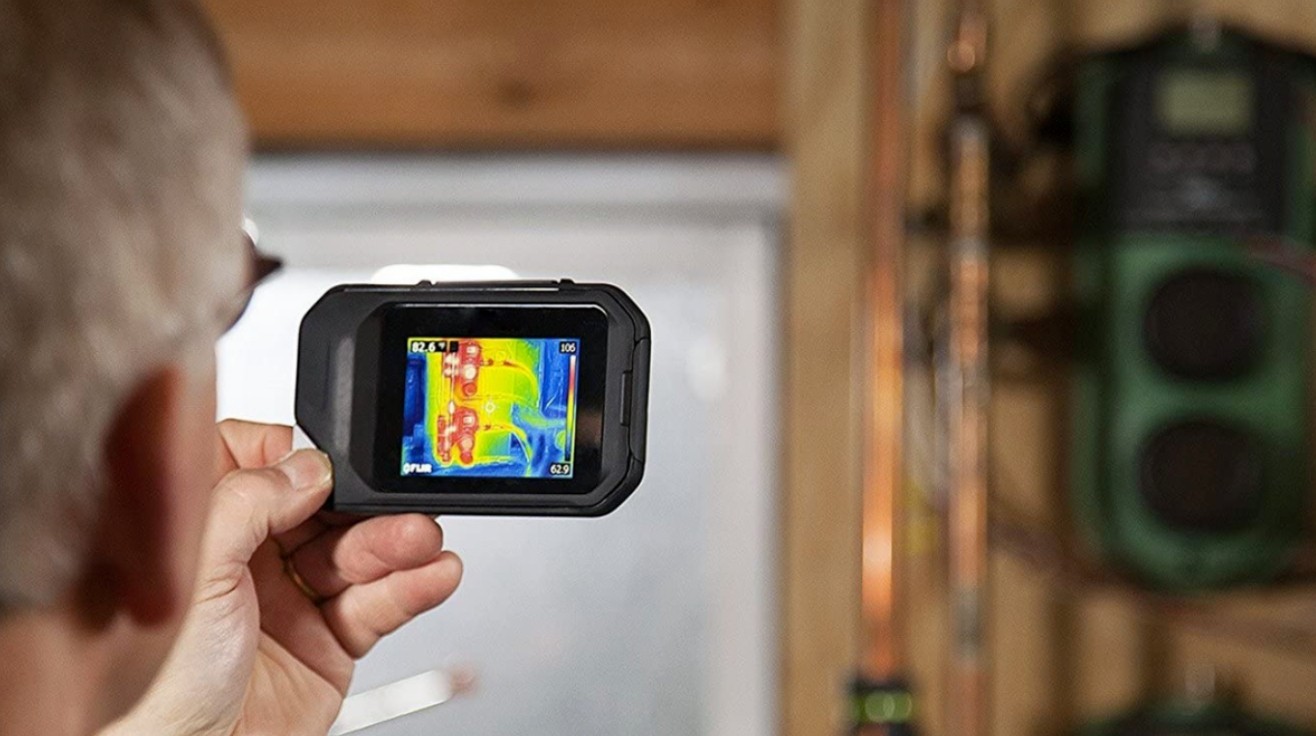
Thermal imaging cameras have revolutionized various industries with their ability to capture thermal radiation and convert it into visible images. The welding and metal additive manufacturing industries are no exception. These innovative devices bring new levels of efficiency and safety to these processes, improving output quality and reducing costs. In this article, we take a deep dive into the significant impact thermal cameras have on welding and metal additive manufacturing processes.
Learn About Thermal Imaging Cameras
What is a Thermal Imager?
A thermal imager, also known as an infrared camera or a thermal imaging camera, is an advanced imaging device capable of detecting and capturing the temperature distribution of objects and scenes. Unlike traditional cameras, which rely on visible light, thermal imaging cameras work in the infrared spectrum. They generate images called thermograms, in which different colors or shades represent different temperatures.
How Does a Thermal Imaging Camera Work?
Thermal imaging cameras work by detecting infrared radiation emitted by objects. Every object with a temperature above absolute zero emits infrared radiation. The camera's sensor detects this radiation and converts it into an electrical signal. The signal is then processed and turned into a visual representation, allowing us to see temperature differences within the scene.
Application of Thermal Imager in Welding
Inspection Before Welding
Before starting the welding process, it is crucial to inspect the materials and components involved. Thermal imaging cameras provide a non-destructive method of identifying defects in weld areas such as cracks or irregularities. This helps the welder ensure that the material is in top condition and that the welding process is successful.
In-Process Monitoring
During the welding process, the thermal imager can monitor the temperature distribution and heat-affected zone in real time. This valuable data enables welders to make necessary adjustments to welding parameters, ensuring consistent and high-quality welds.
Post-Weld Quality Control
After the welding process is complete, a thermal imaging camera can be used to inspect the completed weld. By identifying any temperature anomalies or defects, welders can take immediate corrective action, reducing the likelihood of post-weld failures.
Advantages of Thermal Imaging Cameras in Welding
Improve Security
The welding process involves high temperatures and potentially hazardous conditions. Thermal imaging cameras allow welders to identify hot spots and potential safety hazards, thereby minimizing the risk of accidents and injuries.
Improve Efficiency
Thermal imaging cameras allow for faster, more accurate inspections, reducing the time spent on manual inspections. This efficiency increases productivity and saves costs in the long run.
Cut Costs
By detecting defects early in the welding process, thermal imaging cameras help avoid costly rework and material waste. Additionally, the ability to optimize welding parameters reduces energy consumption and material usage.
Thermal Imaging Cameras in Metal Additive Manufacturing
Monitor the Printing Process
In metal additive manufacturing (commonly known as 3D metal printing), thermal imaging cameras are used to monitor the printing process. These cameras capture the temperature distribution of the printed layer, ensuring that the correct temperature is maintained for successful metal fusion.
Detect Defects and Inconsistencies
Thermal imaging cameras play a key role in detecting defects such as voids and cracks during metal additive manufacturing. Early detection enables manufacturers to correct these issues in a timely manner, thereby improving overall product quality.
Advantages of Thermal Cameras in Metal Additive Manufacturing
Quality Assurance
Thermal imaging cameras enhance the quality assurance process of metal additive manufacturing by providing real-time feedback of printing parameters. This ensures that the final product meets the required quality standards.
Process Optimization
Using data collected by thermal imaging cameras, manufacturers can analyze and optimize metal additive manufacturing processes for greater efficiency and cost-effectiveness.
Challenges and Limitations
Interpretation of Thermal Data
Accurately interpreting thermal data requires a technician with in-depth knowledge of thermal imaging and manufacturing processes. Misunderstandings can lead to wrong conclusions and incorrect adjustments.
The Cost of a Thermal Imaging Camera System
Thermal imaging camera systems can be relatively expensive, especially for small businesses. However, long-term gains often exceed the initial investment.
Future Trends and Developments
As technology advances, we can expect further improvements in thermal imaging cameras, making them more accessible and affordable for various industries. The integration of artificial intelligence and machine learning algorithms may enhance the interpretation and analysis of thermal data.
Buy Thermal Imaging Cameras from JavolVision
JavolVision is a professional custom infrared thermal imaging equipment manufacturer. Our main direction is focal plane imaging core and devices, intelligent optoelectronic system solutions based on multi-spectral and multi-range fusion imaging systems. At present, our company has launched a series of wide spectrum cameras; thermal imaging (LWIR) cores and cameras; and SWIR cores and cameras and systems, which have been integrated into optoelectronic loads. If you want to buy infrared thermal imaging equipment, please contact us.
In Conclusion
Thermal imaging cameras have been a game changer in welding and metal additive manufacturing. Their ability to provide real-time temperature data and detect defects significantly improves the overall quality, safety, and efficiency of these processes. As technology continues to advance, thermal cameras will play an even more important role in shaping the future of these industries.
Frequently Asked Questions
Q: Can thermal imaging cameras be used for other applications besides welding and metal additive manufacturing?
A: Yes, thermal imaging cameras are used in a variety of applications, including building inspections, electrical diagnostics, and surveillance.
Q: Do thermal imaging cameras require special training to use effectively?
A: Yes, proper training is critical for the accurate interpretation of thermal data and the effective use of cameras.
Q: Can thermal imaging cameras detect defects in hidden areas during welding?
A: Yes, thermal cameras can detect temperature anomalies even in hard-to-reach or obscured areas.
Q: Are thermal imaging cameras suitable for mass manufacturing processes?
A: Of course, thermal imaging cameras are scalable and can be used effectively in both small and large-scale manufacturing.
Q: How can thermal cameras help save costs in metal additive manufacturing?
A: Thermal imaging helps reduce material waste and rework costs by detecting defects early and optimizing process parameters.